SIPs factory process involves injecting polyurethane into hollow molds which are made from recycled galvanized steel, mounted on forms and compressed. This recycled galvanized steel meets US building standards for cold-rolled formed steel guidelines. It is structural certified code compliant. The number and size of the panels are created in accordance with the architectural plans.
The electrical tubes inserted into the panels are done in accordance with local building codes. SIPs houses are approved in all 50 states, with variances in the levels that can be built. SIPs panels can be used for commercial buildings as well as residential housing
The most common foundation for a SIPs house is a concrete slab on grade, with plumbing pipes and electrical wiring pulled out. It takes about two weeks to build this base. Basements can be built, but they significantly raise the cost and time to build. Lines for plumbing and electricity are pulled up from the foundation.

An unskilled crew of six workers can build a SIPs house in three days or less. The interior can be framed with steel or wood, then covered with sheet rock and painted. The exterior can be made of any type of material: brick, siding stone or stucco.
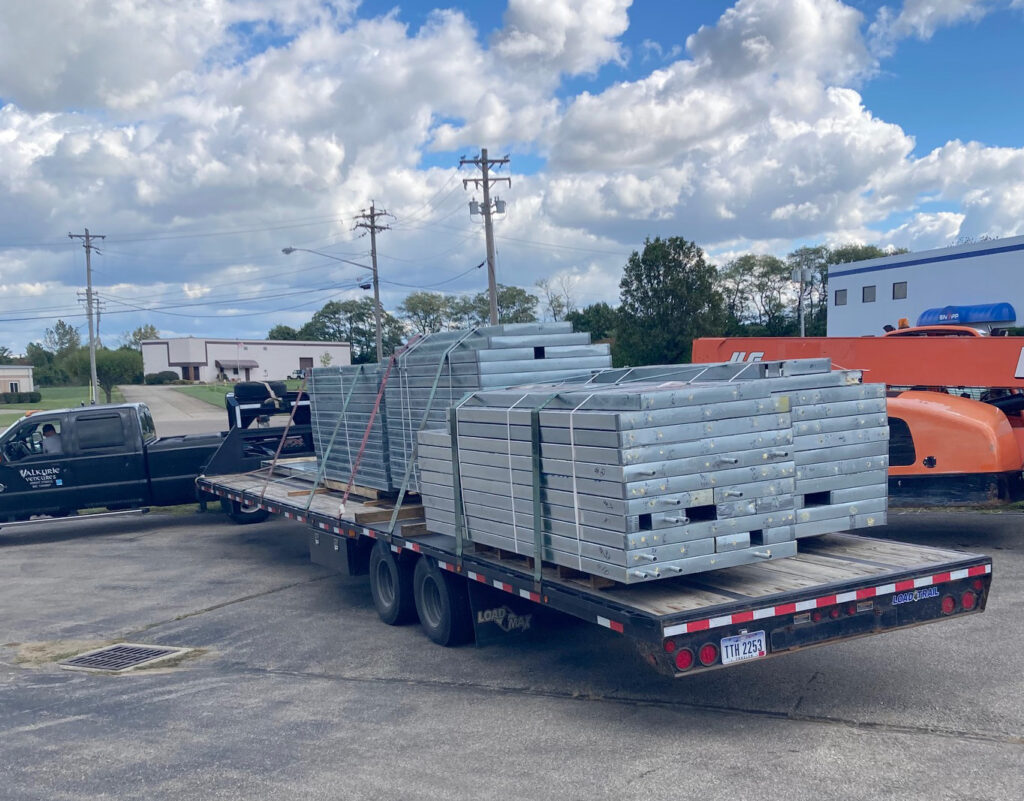
The panels are taken by a flatbed truck to the site, along with the tools needed to mount the panels. The tools are basic, such as nail guns, nails, glue, tape measure and level. For more information on SIPs click here.

Benefits of SIPs over conventional housing
The finished product is indistinguishable from a stick-built house. It can withstand winds of up to 170 miles per hour and has a minimum R-value of 24.5 (nearly twice that of a stick-built house). That means it holds its temperature resulting in lower energy costs for consumers.
Furthermore, it is rodent resistant, as the polyurethane injected into the panels is treated to repel rodents, estimated to last a minimum of 200 years, and is also completely recyclable.
The average cost of a 1,500 square foot house is estimated to be 20,000 less than a stick built due to fewer workers needed to build, less construction materials used (less construction waste) and built-in insulation. Savings are best realized when the houses are constructed at scale.